Supply Chain World magazine
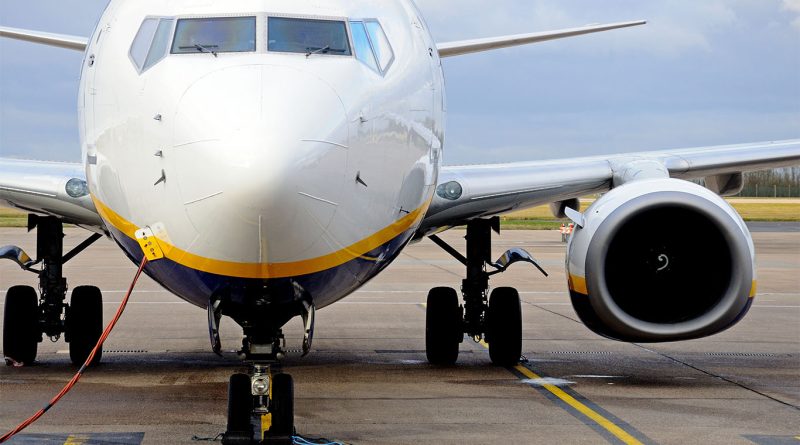

Boeing’s Costly Outsourcing Flight Path
At the turn of the 21st century, Boeing embarked on a bold strategy with the development of the 787 Dreamliner, aiming to revolutionize the aviation industry through extensive outsourcing. The objective was clear: reduce costs, accelerate production, and leverage the expertise of global partners. This strategic pivot sought to transform Boeing’s operational model, capitalizing on the efficiencies and innovations offered by a diverse supplier network spanning continents. However, the endeavor to reshape aerospace manufacturing through outsourcing was fraught with complexities and unforeseen challenges, casting a shadow over the anticipated benefits of this expansive global collaboration.
The Turbulent Skies of Global Supply Chains
Boeing’s foray into extensive outsourcing introduced a level of complexity that would test the resilience and adaptability of its supply chain. With over 50 suppliers from around the globe contributing to the 787 Dreamliner, coordination and quality control became Herculean tasks. This vast network, while a testament to globalization’s potential, also exposed Boeing to risks of delays, quality discrepancies, and communication barriers. The consequences were significant, with the Dreamliner’s launch marred by setbacks, including technical issues that led to an emergency landing during a test flight due to an unexpected fire. These challenges underscored the perils of over-reliance on a fragmented supply chain, where the intricacies of integrating components from myriad sources could jeopardize not just timelines but the very safety and reliability of the end product.
Comparative Turbulence: Boeing vs. Airbus
The contrasting approaches of Boeing and Airbus to outsourcing offer a lens through which to examine the strategic choices in aerospace manufacturing. While Boeing pursued a path of extensive outsourcing, Airbus has opted for a more balanced approach, emphasizing greater control over its supply chain. This strategy has enabled Airbus to maintain a more consistent and reliable flow of materials and components, minimizing disruptions and safeguarding quality. The tale of these two giants serves as a cautionary narrative on the risks and rewards of outsourcing strategies, highlighting the delicate balance between leveraging global capabilities and retaining sufficient control to ensure product integrity and supply chain resilience.
Navigating Back to Calmer Waters
In the wake of the challenges faced with the 787 Dreamliner and 737 MAX, Boeing has initiated a strategic reassessment of its outsourcing model. Acknowledging the pitfalls of overextending its supply chain, the company is now focused on bringing more work in-house, a move aimed at regaining control over critical processes and enhancing the integration and oversight of its supplier network. This shift signifies a broader recognition of the need for a balanced approach to outsourcing—one that weighs the advantages of global collaboration against the imperative of maintaining quality, safety, and reliability. Through strengthened partnerships, rigorous supplier vetting, and enhanced communication channels, Boeing aims to fortify its supply chain, ensuring that future endeavors are grounded in lessons learned from past experiences.
Reflecting on the Horizon
Boeing’s journey through the complexities of outsourcing in aerospace manufacturing offers valuable insights into the dynamics of global supply chains. As the company charts a course towards recovery and growth, the lessons gleaned from the Dreamliner and 737 MAX projects will undoubtedly influence its strategic decisions, guiding a more measured and mindful approach to outsourcing. For the aviation industry and beyond, Boeing’s experience serves as a pivotal case study on the importance of balancing global collaboration with strategic oversight, underscoring the need for resilience, adaptability, and control in the ever-evolving landscape of international manufacturing.
In sum, Boeing’s outsourcing saga, marked by ambition and adversity, provides a compelling narrative on the intricacies of global supply chain management. As the company looks to the future, embracing a philosophy of cautious optimism and informed strategy, the aerospace sector watches closely, poised to learn from Boeing’s endeavors to navigate the turbulent skies of global outsourcing.
- Simple Flying: Looking Back: Boeing Repeatedly Burned By Outsourcing
- Supply Chain Magazine: The Boeing 787 Dreamliner: A tale of TERRIBLE supply chain management
- IndustryWeek: Boeing’s 737 Max Software Outsourced to $9-an-Hour Engineers
- ← S&P Global Strategies for Future-Proofing Global Supply Chains
- U.S., Japan, and India Forge New Paths in Defense →
How Supply Chain Woes are Impacting the Global Aviation Industry
Airbus, Boeing and every major aviation industry OEM is facing supply chain challenges these days.

As the global aviation industry recovers from the COVID-19 pandemic, there is optimism that better times are ahead. But there is a big caveat. Supply chains are reeling, and suppliers to aerospace manufacturers face a host of uncertainties that make finding a solution problematic, especially in the near term.
“I think we’re going to continue to be unstable at least through next year,” David Wireman, global co-head of the aerospace, defense and aviation practice at AlixPartners, told Avionics International . “There are waves of [supply-chain] issues.”
The two companies putting the most pressure on the aviation supply chain are Airbus and Boeing. And each presents a particular challenge to parts suppliers, many of which feed both companies’ manufacturing lines.
Airbus is planning to ramp up its A320 family aircraft production rate from 45 per month in the 2021 fourth quarter to 65 per month by the middle of 2023, and is considering going all the way to 70-75 per month by 2024. This is a steep slope for the company’s supply chain.

“We see some concern with the idea that we’re going to have significant production rate increases,” Glenn McDonald, a senior associate at AeroDynamic Advisory, said in an interview. “It’s harder to ramp up than ramp down–there is a lot of preparation needed.”
Wireman noted: “Airbus is projecting ramp rates they’ve never achieved before in terms of slope.”
Airbus is aware of the supply-chain challenges, but ramping up narrowbody aircraft production is at “the heart of our priorities,” Airbus CEO Guillaume Faury told reporters at a February press briefing.
He conceded that raising production rates will be a “complex” challenge for suppliers. “We see difficulties with raw materials, with logistics, with cost of energy and also with hiring people back across the globe,” Faury said.
Airbus is committed to moving to a monthly A320 production rate of 65 next year, but has not yet decided about going higher. “We need to look at the balance between demand and supply and the ability of the supply chain to accelerate at a certain pace,” Faury said. “We’re still discussing 70, 75 [per month], but we want to look at the stability of the [supply-chain] system.”
The uncertainties bedeviling supply chains are not easy to solve because there are so many issues to contend with, he added. “In terms of resources, it depends on each and every supplier,” Faury said. “The bottlenecks and the challenges are not the same by commodity, by region, by type of equipment, systems and parts we are buying.”

While suppliers are facing a myriad of snags, it is widely agreed that finding enough skilled labor is the most significant obstacle to overcome. “Labor is the big one,” McDonald said.
“Everybody down-sized labor pretty dramatically and now has to decide when to hire and how to find and train workers,” Wireman said. “There’s still a degree of craftsmanship in aircraft manufacturing, so filing a spot doesn’t mean you have expertise. There’s a whole learning curve, sometimes taking years.”
Faury agreed that the labor shortage is serious. “More than the rest [of the supply-chain problems], the ability to find … the human resources in quantity and quality” is critical, he said, adding: “We need the right skills at the right place at the right moment. This is an area where many companies are struggling around the globe. So, we need to factor this in when we define the ramp up plans because we need to be able to execute the ramp up plans.”
But at least Airbus is providing clarity for suppliers. They know the ramp up is coming and when.
Boeing, on the other hand, has had well documented difficulties with its 737 MAX and 787 programs. The MAX reentered service last year after two fatal accidents led to a lengthy grounding, but new 787 deliveries remain suspended, though hundreds of previously delivered 787s are in service with airlines around the world. Further complicating the return of 787 deliveries was the FAA’s announcement in February that the agency–not Boeing–will clear each new 787 before it is delivered.
Long delays in 737 and 787 production present two main challenges for suppliers: Boeing has a huge overhang of already-built parts in inventory and, particularly with the 787, there remains a lack of certainty around future production.
In part because of the inventory overhang, “supply constraints to date have not constrained us,” Boeing CEO Dave Calhoun said in a February conference call with analysts. “On the other hand, I think in the medium- to long-term future, it's something we all have to plan for. I've always viewed the unfortunate means by which we got here and the buildup of finished goods inventory, both with respect to the MAX and the 787, as sort of a double-edged sword. I hate that we have a lot of inventory.”

Wireman believes suppliers “are more likely to invest in Airbus because there is just more clarity” regarding future production. He added: “Boeing is doing everything they can to provide clarity, but every supplier interprets the outlook of [the 737 and 787] programs and the veracity of the signals Boeing is sending differently. Nobody has a clear picture of what their inventory overhang is. Resynchronizing the Boeing supply chain is going to be a challenge and not everyone is going to get it right.”
McDonald noted that Boeing “has a more measured production ramp up”–seeking to go from a MAX production rate of 19 per month in 2021 to 31 per month this year–that alleviates some pressure.
“With our production at relatively low rates and higher-than-normal inventory levels, the supply chain is currently not a constraint,” Boeing CFO Brian West said. “However, as we look forward to the industry recovering and future production rate increases, our supply chain remains a key watch item due to raw material and labor availability as well as logistical challenges.”
Of course, it is not just Airbus and Boeing that are dealing with supply-chain concerns. The problems cascade throughout the aerospace industry, hitting companies such as single-engine light aircraft manufacturer Cirrus Aircraft.
“We’ve had a quick pivot to a high-demand scenario,” Cirrus President-Innovation & Operations Patrick Waddick told Avionics. “Labor availability has had one of the greatest impacts. Workforce issues have really hampered supply chains.”

As a result, lead times on electrical components, for example, have “expanded significantly,” he said, explaining that the typical lead time has grown from 18 weeks to 30 weeks.
Cirrus is also being heavily affected by the congestion at ports. “We export airplanes by container ship to China,” Waddick said. “We’ve had aircraft in shipping containers sitting on boats for months. This is just a perfect storm. It’s as challenging a situation as I’ve seen in my career. It’s going to take some time for these issues to stabilize. We’re talking about building highly technical systems that require significant investment and lead time.”
There is generally hope that aerospace supply chain bottlenecks will begin to alleviate next year. “You can see your way to brighter times in ‘23 or ‘24 without any major new hiccups,” Wireman said. “It’s really an interesting time because there are some significant unknowns.”

March/April 2022

COVID-19, Labor Force and Supply Chain
The aviation industry continues to deal with uncertainty on a number…
A look at how supply chain challenges are impacting different areas of…

AAR Corp Embracing Digital Transformation, Drones, and Increasing Demand for Connectivity in Commercial and Military Aviation
Our interview with AAR Corp. VP Matt Kammerait.

Aviation Industry Adjusts to Increasing Demand for Aircraft Maintenance Technicians
Aircraft maintenance jobs are in high demand.

Special Feature: Recent Industry Updates on Commercial Aircraft Values
A special feature from Aircraft Value News.

FEAM Chief Strategy Officer Talks Maintenance for Cargo Planes and Expanding in a Pandemic
A Q&A with MRO company FEAM.

United Selects Cirrus TRAC SR20 with Airliner-Style Avionics for New Flight Training Academy
United Aviation Academy has a new fleet of training aircraft.

OPINION: Four Strategies to Help Airlines Manage and Mitigate Supply Risks
Airlines and the global supply chain.

Coming Up May/June 2022
Coming up in our May/June 2022 issue.
Supply Chain Quality Management within the Aeronautical Industry
Case study at the airbus single aisle fuselage assembly.
Contributors
Published Date
Reuse Rights
Other than for strictly personal use, it is not permitted to download, forward or distribute the text or part of it, without the consent of the author(s) and/or copyright holder(s), unless the work is under an open content license such as Creative Commons.
Within the aeronautical industry product quality is an inevitable key factor to guarantee safety and customer satisfaction. In the last years the increasing complexity of modern aircraft, however, has led to an immense demand for collaboration of different manufacturers in order to stay competitive. Therefore, there is an increasing interest in establishing effective supply chains and ensuring not only internal quality, but also applying existing quality management principles and instruments on the whole supply chain. In order to contribute to the recent developments in the emerging research field of supply chain quality management, this master thesis follows a twofold approach by first, reviewing the current state of the art and pointing out the derived best practices and, second, conducting a case study at the Airbus Single Aisle fuselage production, hereby analyzing the industrial processes and making recommendations on how to improve the existing Airbus processes. The in-depth knowledge acquired during the case study helps to understand how the aeronautical industry strives to fulfill the authority requirements and customer expectations in terms of product quality and how the existing quality management methodology is applied and expanded into the growing supply chains of aircraft manufacturers. In addition, the developed methodology and the identified factors for effective supply chain quality management as well as the weaknesses and strengths of the applied processes provide a foundation for further research within this field.
- DSpace@MIT Home
- MIT Libraries
- Graduate Theses
A comparative analysis of supply chain management practices by Boeing and Airbus : long-term strategic implications
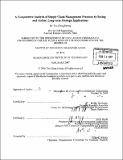
Other Contributors
Terms of use, description, date issued, collections.
Show Statistical Information
We use necessary cookies that allow our site to work. We also set optional cookies that help us improve our website.
For more information about the types of cookies we use, and to manage your preferences, visit our Cookies policy here.
Impact story
Case study: The value of sharing data in supply chain optimisation
How Airbus shares engineering data on its aeroplane concepts with supply-chain partners to improve the efficiency and accuracy of its product design
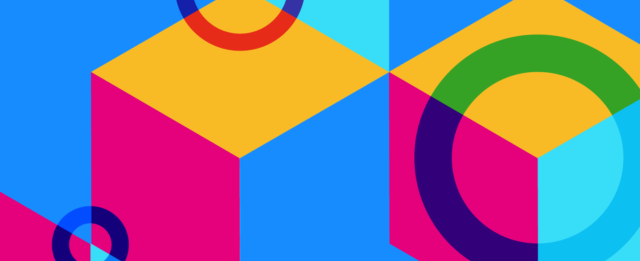
Tue Mar 3, 2020
In this case study we look at how Airbus shares engineering data on its aeroplane concepts with supply-chain partners to improve the efficiency and accuracy of its product design.
This case study is part of a project exploring the value of data sharing in the private sector. When sharing data, businesses face a range of challenges. A significant barrier is a lack of understanding of how increasing access to data can create business value, for example, by enabling new business models, increasing efficiency or reducing costs.
To help address this, we have been documenting real-world examples of how the private sector is creating value from increasing access to data.
Key findings
- Sharing data across the supply chain is a growing trend and a key part of Industry 4.0.
- Sharing trusted data allows aerospace manufacturing to become much more efficient – design processes that used to require weeks to complete can now be completed in a matter of hours.
- Airbus teamed up with its supply chain partners to develop a proof-of-concept data sharing platform within the collaborative research project APROCONE.
- The aim was to increase supply chain efficiency and reduce aircraft development costs for manufacturers like Airbus.
- Creating a secure and efficient means to share data has helped companies like Airbus engage with new technology providers and researchers to support innovation as well as optimise supply chains.
- Improvements in supply chain optimisation are leading to more environmentally friendly outcomes with the intent to reduce the industry’s carbon footprint.
Read the full case study
Many businesses are embracing the sharing of data, and are seeing tangible benefits for their organisations and across their entire sectors. Josh D’Addario , Consultant at the ODI, has been talking to these organisations and researching the benefits. Josh shares his top seven reasons why businesses should be sharing data.
Read article
The ODI is engaging with private-sector companies to show how sharing data can positively impact the bottom line.
We are already seeing open approaches to data happening in sectors such as physical activity, banking, and pharmaceuticals.
This project seeks to demonstrate the business value of sharing data to a sector, network or individual business, looking at how an organisation might benefit in terms of innovation, network capabilities, and brand positioning.
Find out more
Get in touch with our team to discuss the potential for your organisation to get more from data, join our events and follow our research
We’re currently developing a toolkit to help people working in the private sector to plan their data sharing strategies. It is due to be created by the end of March, so please share your details below to receive the toolkit when it’s ready.
Other case studies for sharing data in the private sector
Supply chain integration in aviation: AirSupply case study
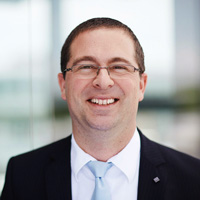
Airlines, aircraft manufacturers and their suppliers have been confronted with fundamental challenges in the past few decades – with far reaching effects on their entire supply chains. From individual interiors and exteriors configuration to component development through to aftermarkets. These are the core issues of this book, analyzed by a series of industry and research experts and giving the reader a holistic view of not only the transformation drivers but also of past, current and future innovations.
AirSupply as a Best Practice for Supply Chain Integration
AirSupply is presented as one of the key examples of how solve the challenges of supply chain integration. The solution was developed by Su0pplyOn in cooperation with Airbus, Dassault, Safran and Thales, all leading manufacturers and suppliers of the European aviation and aerospace industry. AirSupply incorporates aerospace and defense supply chains within a single tool, therefore enabling maximum transparency throughout all central supply chain management processes. Bottlenecks can be recognized at an early stage, inventory optimized, on-time delivery improved and customer satisfaction increased.
This book was published by Johannes Walter from the Institute for Production Management (IPM) and Dr. Klaus Richter, Chief Procurement Officer at Airbus Group. It will be released in mid-December 2016 and can be ordered on Amazon .
read more from
As Sales Manager, my goal is to be the central point of contact for our new aerospace customers, but also for customers from other industries, and to advise them as best as possible on a solution design that fits their needs as well as to accompany them not only until the contract is signed, but also until the start of productive use. It is important to me to ensure that new customers are handed over to our Delivery department and then to our Consulting team. Customers should not only feel that they are in good hands during the ongoing project, but also when new challenges arise that affect them and where SupplyOn can be part of the solution. In addition to regular exchanges via modern communication media, personal exchanges with my contacts are particularly important to me — at trade fairs, at customer meetings and, of course, at the customer's site. I mainly blog about aerospace trade fairs and customer meetings.
Matching themes:
- digital supply chain
- supplier collaboration
More articles on this topic
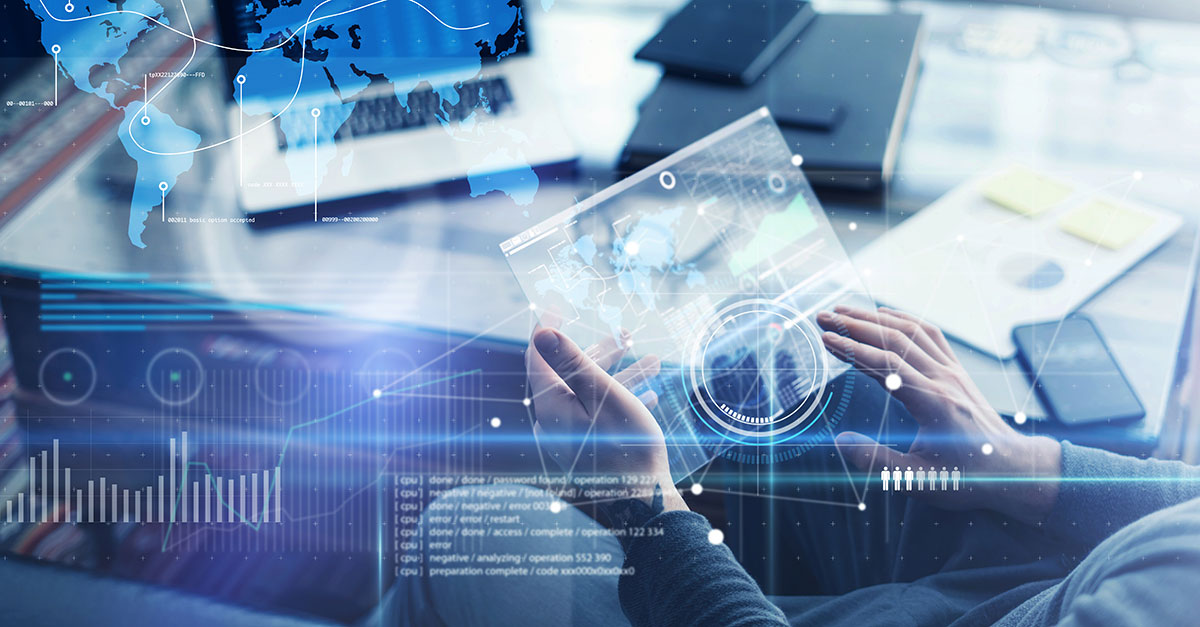
Supplier Performance Management: how to systematically strengthen your supply chain
You can only manage what you measure, they say—and rightly so. This is especially true when it comes to supply chain performance. Disruptive change and increasing demands for cost efficiency, quality, and speed present unique challenges. Only by measuring how well it is performing can the supply chain be properly aligned and optimized.This requires a…
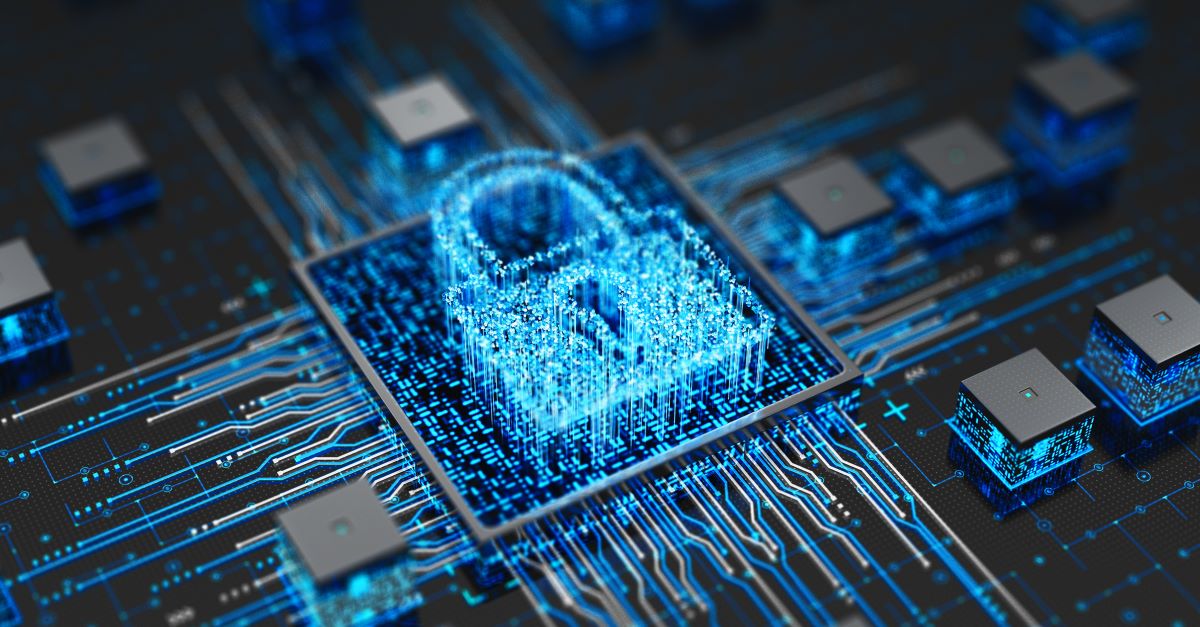
Business Continuity: Contingency plan in case your supplier is the victim of a cyber attack
Unfortunately, cybercriminals continue to gain access to corporate IT infrastructure, encrypt data, and then demand large sums of money to “decrypt” it. The impact on affected companies is devastating! It often takes several months before they can operate as they did before the attack.Even if your company has planned for this eventuality: What if one…
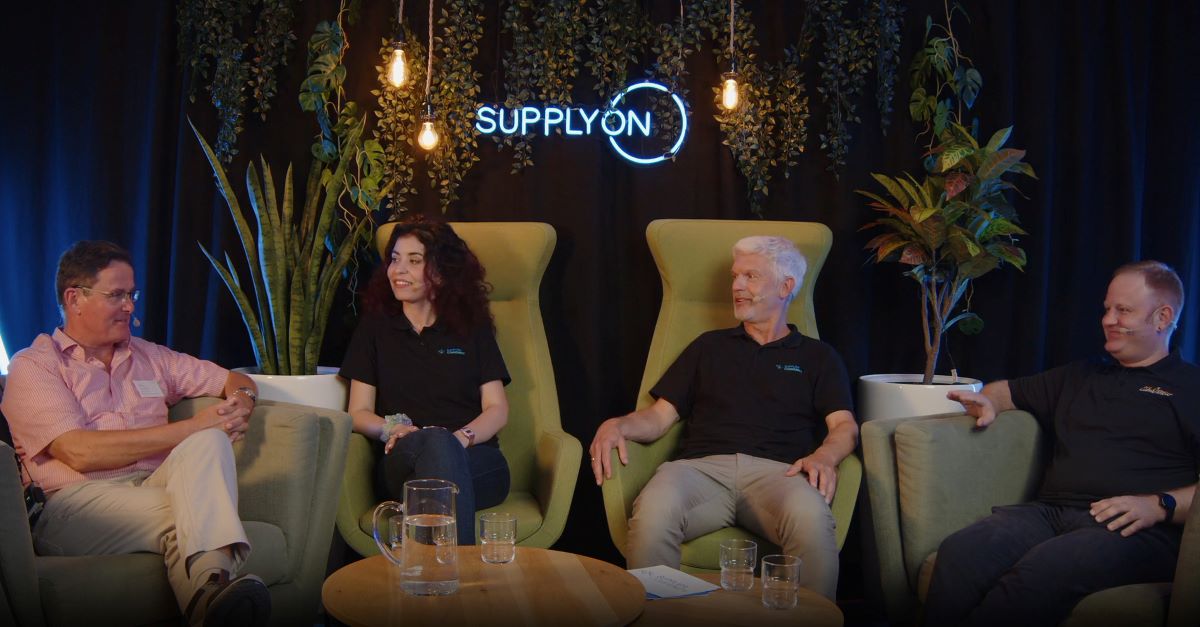
Introducing Performance Management for enhanced collaboration
On a vibrant and enlightening Supplier Community Event, industry professionals gathered to witness the unveiling of the new cutting-edge SupplyOn Performance Management. The event was designed to introduce this innovative solution, offer a sneak preview, and host a panel discussion with esteemed speakers from Bosch, ZF and Klüber Lubrication. This blog delves into the highlights…
Capturing Latent, At-Risk Knowledge

- BOXARR Marketing
- Mar 21, 2019

Overcoming Complexity in a Global Aerospace supply chain
Updated: Mar 16, 2023
CASE STUDY | Airbus Commercial Aircraft
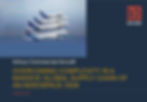
Introduction
Businesses face many hazards – from currency gyrations, regulatory compliance difficulties, geopolitical changes to natural disasters, and constantly changing customer needs. This Case Study describes the management of the global supply chain for an aerospace OEM, so the case relates most specifically to the delivery of aircraft. However, the problem is generic across many products, services, and verticals, where supply chains are massive and complex. Moreover, it relates to other complex sequential processes that have characteristics similar to supply chains (e.g., value stream maps, production processes, etc.).
In This Case Study You Will Learn
How BOXARR can manage massive scale (hundreds of thousands of boxes, millions of data objects).
How a BOXARR model can be created and updated by information from multiple data sources (and information can be roundtripped from BOXARR to other sources).
That BOXARR models designed to solve one problem can become permanent information artefacts that can be adapted to other critical business problems.
How functions and macros can supplement BOXARR models to facilitate critical workflows for understanding and managing complexity, saving time and money, and reducing risk.
How benefits from BOXARR models can be distributed to a broad audience within an enterprise via nSight, thus leveraging enterprise insights into complexity.
Our Customer
Airbus is an industry-leading manufacturer and designer of aerospace products, services and solutions to customers on a global scale. The company is one of only two international heavy commercial aircraft OEMs and is the largest aerospace corporation in Europe.
Airbus has built on its strong European heritage to become truly international – with roughly 180 locations and 12,000 direct suppliers globally. The company has aircraft and helicopter final assembly lines across Asia, Europe, and the Americas, and has achieved a more than sixfold order book increase since 2000. Over the last 45 years, Airbus has built a reputation by reacting to market demands, developing and evolving its products to meet the needs of its customers and the wider world. As such, technological innovation has been at the core of Airbus’ strategy since its creation.
Their Challenge
The collision of unprecedented complexity and time criticality
Supply Chain Mapping
Airbus commercial aircraft may have the largest, most globalised, and most complex supply chain in the world. The enormous complexity of the Airbus civil aircraft manufacturing supply chain means it is very difficult to have an overview let alone understand all the stakeholders involved in a given value chain, not to mention the relationships that these suppliers have with other suppliers. As such it is difficult to quickly identify the impact of any disturbance in the supply chain or to identify those suppliers who are at higher risk.
For example, some suppliers will have a great number of dependencies in the supply chain, or they might be subject to a potential geopolitical risk, or they could provide their components across multiple aircraft programmes.
On-Time Delivery
Also, the delivery of their product is on the schedule of almost unprecedented criticality. Disruptions to that delivery can cost tens of thousands of euros per day or more. Airbus wished to speed its response to supply chain emergencies to avoid these potentially devastating costs. They also wanted individuals across their organisation to gain a more general understanding of their supply chain, so that can be better utilized, engineered, and tuned over time.
Expected Outcome
Airbus wished to reduce their response time to supply chain emergencies (which can be caused by economic, environmental, political, and many other factors). They also wished to have a better understanding of their supply chain for a broad spectrum of engineering and planning activities in the future.
Why BOXARR?
After a competitive bid process for tools that could handle this challenge, BOXARR was selected to help, and Airbus team was assigned to work with BOXARR to create the supply chain model. Since that initial engagement, Airbus has dedicated a team to use the model and work with the BOXARR.
The BOXARR Solution
How did BOXARR approach the challenge?
BOXARR worked with the client to understand both their challenges and their existing data sources that would help address them. We helped Airbus to ingest that data to formulate a BOXARR model that can be continuously updated, instrumented to solve Airbus’s particular challenges, and distributed to a large community of Airbus users through our web-based client, nSight.
How was our client involved in this stage?
BOXARR worked closely with an Airbus team to identify data sources and procedures for their utilisation in the BOXARR model.
What was the solution?
Airbus together with BOXARR team built a global supply chain model of massive scale that is managed effectively by BOXARR and a dedicated Airbus supply chain team, which can be used for planning and coping with emergent situations. This model coupled to custom dashboards through nSight, which are tuned to particular user groups, and made available to thousands of users across Airbus.
What was the timeline?
The initial creation of the model took place over a scale of weeks
Annualized Return on Investment

If you would like to know more about the Case Study please contact us.
Recent Posts
What are Supply Chain Risk Overlays?
Understanding Heat Mapping
Understanding Supply Chain Risk Overlays
- Work & Careers
- Life & Arts
Airbus chief says supply chain crisis will last until 2023
To read this article for free, register now.
Once registered, you can: • Read free articles • Get our Editor's Digest and other newsletters • Follow topics and set up personalised events • Access Alphaville: our popular markets and finance blog
Explore more offers.
Then $75 per month. Complete digital access to quality FT journalism. Cancel anytime during your trial.
FT Digital Edition
Today's FT newspaper for easy reading on any device. This does not include ft.com or FT App access.
- Global news & analysis
- Expert opinion
Standard Digital
Essential digital access to quality FT journalism on any device. Pay a year upfront and save 20%.
- FT App on Android & iOS
- FT Edit app
- FirstFT: the day's biggest stories
- 20+ curated newsletters
- Follow topics & set alerts with myFT
- FT Videos & Podcasts
Terms & Conditions apply
Explore our full range of subscriptions.
Why the ft.
See why over a million readers pay to read the Financial Times.
What are you looking for?
Most popular topics.
- Sustainable aviation fuel (SAF)
02 September 2024
Developing a global ecosystem to support hydrogen-powered flight.
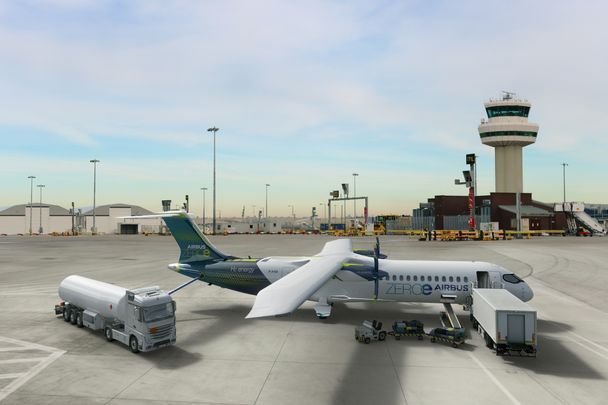
Airbus aims for hydrogen-powered aircraft to enter into service by 2035. While the engineering progress necessary to make this a reality is well underway, there is a second and equally pivotal half of development that must advance in tandem: the creation of a global hydrogen ecosystem.
The argument for hydrogen
Hydrogen is one of the most promising energy sources we have to decarbonise industrial processes. It produces little to no carbon dioxide emissions when used, and when made from renewable energy – known as green hydrogen – its carbon footprint is practically zero.
The cost of green hydrogen is expected to significantly decline as large-scale production accelerates to meet the growing decarbonisation needs of many different industries, applications and usages worldwide. Independent forecasts from the International Energy Agency (IEA), International Renewable Energy Agency (IRENA), and McKinsey predict that cross-industry scale-up will significantly reduce costs.
Indeed, renewable hydrogen will likely be a key factor in decarbonising many industries in the coming decades. But it has a particularly important role to play in helping the aviation industry reach its goal of achieving net-zero CO 2 emissions by 2050. Hydrogen has a specific energy-per-unit mass that is three times higher than traditional jet fuel, making it a much more effective decarbonised energy source than batteries, for example.
Airbus has revealed four different hydrogen-powered aircraft concepts, and announced the goal of having one enter into service by 2035. But while pioneering hydrogen-powered flight technology is obviously the primary goal, securing the supply and distribution of hydrogen at airports is just as important to the success of the programme. What use is a hydrogen-powered aircraft if there are no accessible hydrogen supplies nearby to power it?
Hydrogen Hubs at Airports network
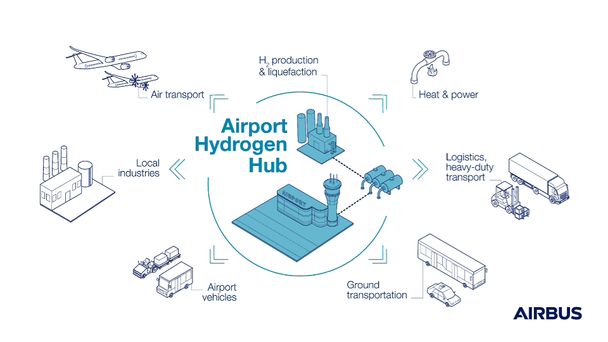
With that in mind, Airbus founded the Hydrogen Hubs at Airports network, a collaborative initiative where the Company is joining forces with airlines, airports, industry partners, energy providers and technology specialists to answer some primary questions: What impact will operating hydrogen-powered aircraft at airports have on infrastructure? Where will hydrogen produced from renewables come from? And how will it be distributed within the region?
To define the answers, Airbus and its partners are investigating the feasibility of hydrogen-powered aviation in terms of developing an ecosystem of decarbonised facilities, ground operations and transportation at airports around the globe. This 360 degree approach looks beyond the airport to take into account other important factors such as where and how green hydrogen is produced, the cost and logistics of hydrogen supply and storage, and what kinds of long-distance pipelines and distribution networks could be necessary.
A walkthrough of an end-to-end hydrogen supply chain
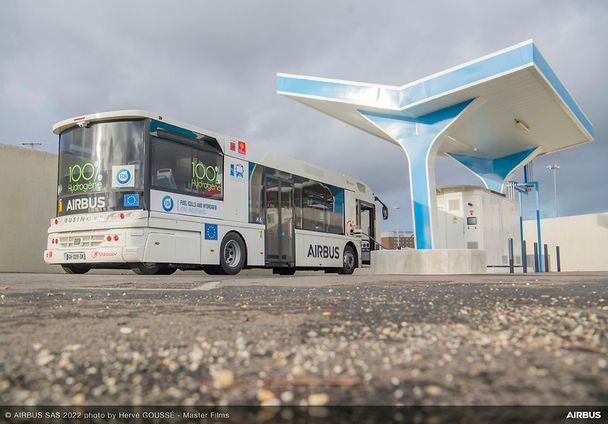
The first challenge to tackle is producing the hydrogen. Green or renewable hydrogen is made through water electrolysis that is powered by renewable or low-carbon electricity. It is the production method with the lowest carbon footprint, and the one that must be used to meet the goal of decarbonising aviation. Renewable hydrogen is first produced in gaseous form, and then liquefied as needed. These steps can be done at the same facility or separate ones.
Once the hydrogen has been produced, it needs to be transported. Several scenarios have been evaluated to supply these airports with liquid hydrogen, taking into consideration operation and cost efficiency. For lower demand, the hydrogen can already be transported in liquid form by truck, and even by ship (tanker ship prototypes are under development). For high levels of hydrogen demand, one economical solution consists of utilising and repurposing existing European and US pipeline networks that could efficiently carry large amounts of gaseous hydrogen over the long distances between the production centre and the airport. The liquefaction process would then take place at or close to the airport. Existing natural gas pipelines could transport hydrogen without requiring major modifications, and there are ambitious plans in both Europe and North America to build up new hydrogen pipeline networks. For example, in Europe, the European Hydrogen Backbone initiative is a masterplan for a continent-wide network of hydrogen infrastructure.
Once the hydrogen arrives at the airport, it would then be stored in highly insulated cylindrical “bullet” tanks. The additional infrastructure needed at this stage includes loading and unloading docks for the trucks, as well as vent masts to evacuate excess boil-off. The liquid hydrogen would then be used to not only power hydrogen aircraft, but ground transportation and airport vehicles as well.
A growing network yields key results
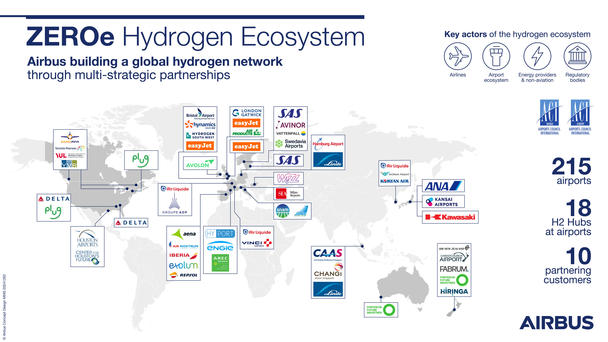
The Airbus hydrogen network currently counts some 215 airports and numerous energy providers and airlines as partners. While new partners are being recruited to join on a regular basis – in July 2024 alone, two Hydrogen Hubs were launched, one in Spain and another at Gatwick airport in the UK – the first partnerships are already yielding preliminary results that provide concrete learnings and guidance for how to best prepare for ZEROe’s entry into service in 2035.
For example, it has already been determined that operating a 100-seat hydrogen-powered aircraft is viable using remote hydrogen production and liquefaction, with airport supply delivered by truck. This supply pattern is the simplest to implement and the easiest to scale. In contrast, supporting 200-seat hydrogen-powered aircraft would ultimately require large-scale hydrogen infrastructure at the airport, as well as proximity to high-voltage power lines or hydrogen pipelines.
Price is also a key factor. While hydrogen has already been deployed at airports for non-aviation use (such as for ground transportation onsite), strong support for initiatives and incentives is still needed to make renewable hydrogen production and transportation economically competitive. Current price studies conducted by Airbus and its partners show a large range of hydrogen prices depending on location and availability of hydrogen production centres.
Finally, airlines themselves are important partners. They have a convening power, acting as network catalysts. Naturally, airlines share the ambition to reach net zero by 2050. This makes them key supporters of all decarbonisation levers, including hydrogen-powered aircraft.
Looking towards the future
There remains much to do between now and 2035 to support hydrogen-powered flight and the corresponding infrastructure on the ground. But the growing number of partners on this project demonstrate that it is not an isolated dream, but a shared one. As society turns to more sustainable energy sources to meet ambitious climate targets, the benefits of renewable hydrogen cannot be overstated. We look forward to welcoming new regions and partners to the Hydrogen Hubs at Airports initiative in the coming years, all working together with one goal in mind: to decarbonise the industry and see ZEROe take flight!
To see how Airbus envisions the future of hydrogen-powered flight, watch the fourth episode of the Countdown to ZEROe Series:
The countdown to ZEROe: Episode 4 : Making the right connection
Airbus' hydrogen-powered aircraft is taking shape. Last time, we talked about one of the most promising propulsion candidates. Discover now how Airbus is building the right hydrogen ecosystem all around the world to fuel our future aircraft by 2035.
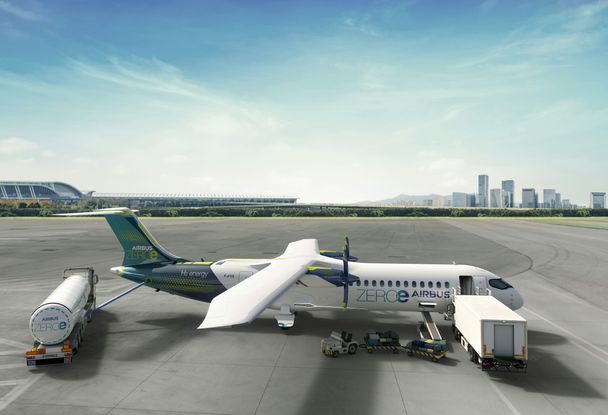
Hydrogen at Airbus
Related news.
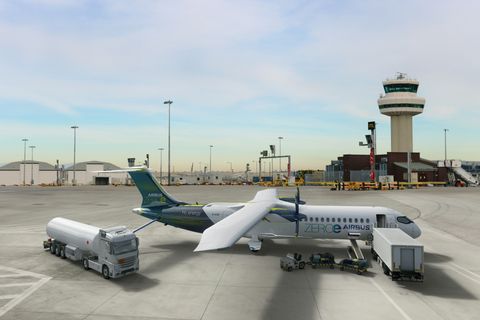
Airbus partners with Avolon to explore future of hydrogen aviation
Airbus welcomes london gatwick to global hydrogen hub network.
- Engineering & Technology
- Industrial Engineering
- Supply Chain Management
Airbus Case Study
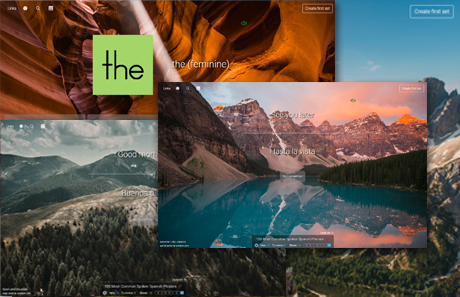
- Distribute all flashcards reviewing into small sessions
- Get inspired with a daily photo
- Import sets from Anki, Quizlet, etc
- Add Active Recall to your learning and get higher grades!
Related documents
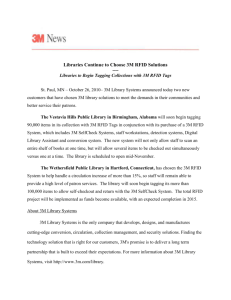
Add this document to collection(s)
You can add this document to your study collection(s)
Add this document to saved
You can add this document to your saved list
Suggest us how to improve StudyLib
(For complaints, use another form )
Input it if you want to receive answer

IMAGES
COMMENTS
supply chain management systems into just one and as a result had earned Airbus a place among the th ree fin alists of the German Logis tics Award mundial in 2019 (Weber, 2019 ).
A hierarchical approach to study supply chain conflicts between Airbus and Boeing. Proceedings of the 2014 IEEE International Conference on Systems, Man, and Cybernetics, 1559-1564.
Comparative Turbulence: Boeing vs. Airbus The contrasting approaches of Boeing and Airbus to outsourcing offer a lens through which to examine the strategic choices in aerospace manufacturing. While Boeing pursued a path of extensive outsourcing, Airbus has opted for a more balanced approach, emphasizing greater control over its supply chain. This strategy has enabled Airbus to maintain a more ...
Airbus, Boeing and every major aviation industry OEM is facing supply chain challenges these days.
The Airbus Group 2014 CR&S report focuses on material issues that have significant operational and strategic impacts, potentially affecting the Group's risks and performance. It includes both key performance indicators and descriptive information, addressing the following topics: Governance, Innovation, People, Supply chain, Philanthropy.
For this purpose, we examined the relationship between Airbus Company and its main suppliers. In a multi-client model in which a company can provide products to multiple customers (multi-customer supply chain inventory model where a company can supply products to multiple customers), it is possible to optimize the supply chain [15].
Purchasing strategy and supply chain management, the Airbus productive system case January 2019 RAIRO - Operations Research 54 (4) DOI: 10.1051/ro/2019014 License CC BY 4.0 Authors: Frédéric Mazaud
A company's environmental and social impact is closely linked to its supply chain. At Airbus, we focus on integrating high standards throughout our operations to foster a responsible supply chain. This includes working to manage natural and human resources in a responsible way at every step of the production process.
sustainable in the Aeronautic industry - Airbus case study David Arturo Pardo Melo To cite this version: David Arturo Pardo Melo. Towards the conception of a Supply Chain efficient and sustainable in ... Jet Engine Manufacturer Supply Chain Case Study (Ramudhin and Benkaddour, 2010) 31 1.3.8. Aircraft Wing Box Case Study (Tang et al., 2013 ...
Opinion: Why Airbus Needs To Update Its Supply Chain Model. Airbus is in a historic position of strength, with the opportunity to become the world's most important aerospace OEM. It is breaking ...
This Case Study describes the management of the global supply chain for an aerospace OEM, and therefore the case relates most specifically to the delivery of aircraft.
In order to contribute to the recent developments in the emerging research field of supply chain quality management, this master thesis follows a twofold approach by first, reviewing the current state of the art and pointing out the derived best practices and, second, conducting a case study at the Airbus Single Aisle fuselage production, hereby analyzing the industrial processes and making ...
Airbus harmonized its global procurement processes with an innovative, highly comprehensive initiative featuring AirSupply, earning a well-deserved nomination for the German Logistics Award. The construction of an aircraft is preceded by a highly complex, sophisticated procurement process. Almost every aircraft at Airbus is unique - and ...
The goal of this research is to develop an improved understanding of supply chain management strategies and practices being pursued by Boeing and Airbus in the 787 Dreamliner and the A380 Navigator programs, respectively, and to identify their long-term strategic implications for supply chain management in the future.
The Airbus case highlights the importance of risk management in global supply chains. All three cases demonstrate examples of benefits and challenges posed by knowledge sharing with partners in ...
In this case study we look at how Airbus shares engineering data on its aeroplane concepts with supply-chain partners to improve the efficiency and accuracy of its product design.
AirSupply as a Best Practice for Supply Chain Integration. AirSupply is presented as one of the key examples of how solve the challenges of supply chain integration. The solution was developed by Su0pplyOn in cooperation with Airbus, Dassault, Safran and Thales, all leading manufacturers and suppliers of the European aviation and aerospace ...
CASE STUDY | Airbus Commercial Aircraft IntroductionBusinesses face many hazards - from currency gyrations, regulatory compliance difficulties, geopolitical changes to natural disasters, and constantly changing customer needs. This Case Study describes the management of the global supply chain for an aerospace OEM, so the case relates most specifically to the delivery of aircraft. However ...
Airbus expects the supply chain crisis gripping the global aerospace industry to last until next year while suppliers struggle to increase production as the world emerges from the pandemic.
Airbus has revealed four different hydrogen-powered aircraft concepts, and announced the goal of having one enter into service by 2035. But while pioneering hydrogen-powered flight technology is obviously the primary goal, securing the supply and distribution of hydrogen at airports is just as important to the success of the programme.
Case Study of Airbus and RFID. Airbus recently introduced a 'maintenance, repair and overhaul' (MRO) strategy supporting RFID adoption for "value chain. visibility," by tracing both flyable and non-flyable components over their total lifecycle. (Sweeney, 2010) According to Carlo K. Nizam, Airbus's head of value chain visibility, the ...